
PELI PELI AUSTIN
Reach Architects | Program: South African Restaurant | 5566 ft2| Status: Permitting
Austin, Texas | Role: Project Manager/Lead Designer | Fall 2016
“The Lord God made all kinds of trees grow out of the ground—trees that
were pleasing to the eye and good for food. In the middle of the garden were
the tree of life and the tree of the knowledge of good and evil.”
--Genesis 2:9
Inspired by the Acacia Tree, the Tree of Life becomes the focal point in most of Chef Paul Friedman's restaurants. The Tree of Life provides the breath of life and nourishment of the soul, which embodies the values of Chef Paul Friedman’s gifts and talents he shares with the 300 people dining in his restaurant. As the roots dig deep into the soul of the earth, the trunk establishes a strong foundation. It embraces the Earth with its roots and recognizes the soil as its mother. In its branches, it reaches out to accept nourishment of the sun. In its leaves, it captures that nourishment and transforms food giving life. As we dine under the canopy at Peli Peli Austin, we are reminded of the importance of The Tree of Life, giving us the first possible natural shelter and bearing its fruit for its inhabitants. Chef Paul Friedman claims as we eat naturally, we are also fed spiritually; to eat from the Tree of Life symbolizes eternity in God’s Paradise.

1. Freeform Surface
2. Panelized Diamond Surface
3. Offset Surface

Grasshopper script for panelized diamond surface

Section A-A
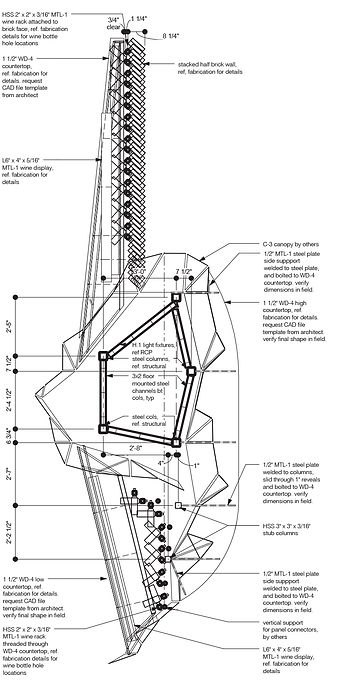
Plan of canopy base
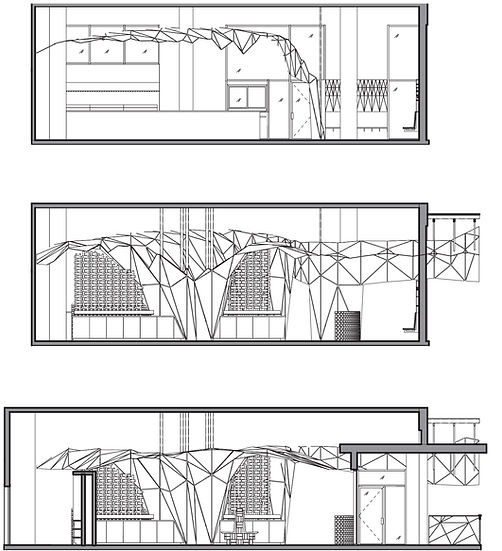
Section B-B
Section C-C
Section D-D

Plan


Approximately 351 birch plywood panels and 65, 12-gauge metal exterior panels
Fabrication and Installation
The canopy is made up of approximately 65, 12-gauge metal exterior panels, while the interior is made up of 351, ¾” birch plywood panels cut out from 5’ x 10’ plywood sheets. As the canopy was laid out, I began to think about how the canopy will begin to be fabrication and installed. Each panel is unique to its own shape and needs to be itemized. I began by splitting the canopy up into 10 manageable sections that has about 30-40 panels. Each section is color coded for the fabricator. A grasshopper script was developed in order to tag each panel with a sequential number, take the panel itself and unroll or flatten the surface. The flattened panels were then laid out on a grid with its respective tagged number. We could then easily count the approximate number of plywood panels needed and the actual square footage of birch plywood needed. This will ease the process for the fabricator as he or she begins to lay out the panels to be cut out by a laser cutter and installed onsite.


Axon Details: Brick @ hostess stand, plant wall, and metal panels @ bar
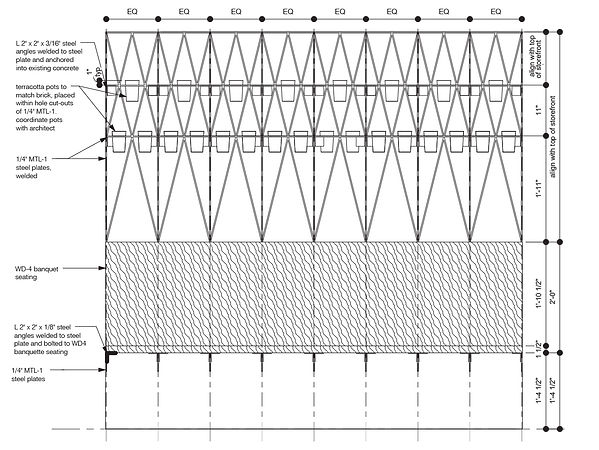
Plant wall @ waiting area

Brick @ hostess stand
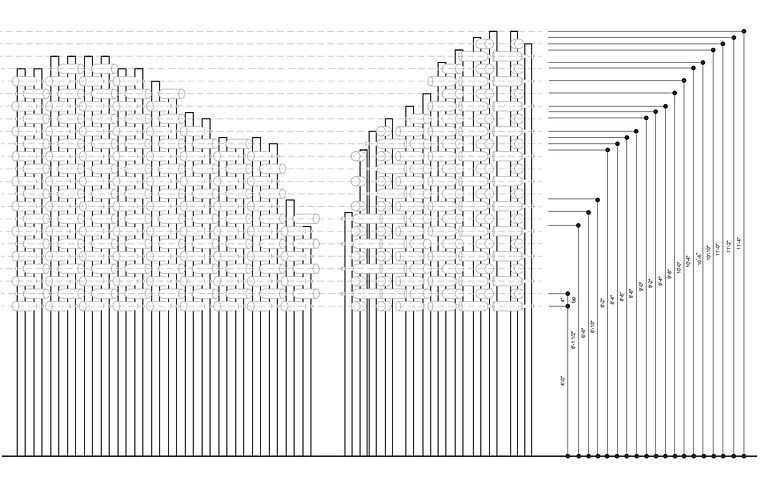
HSS tube wine racks
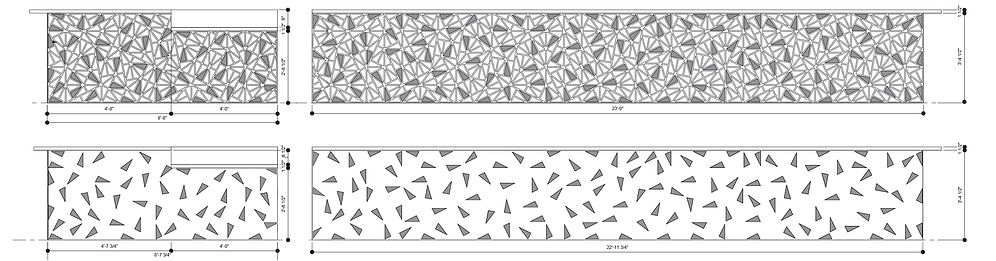
Water jet cut metal panels @ bar
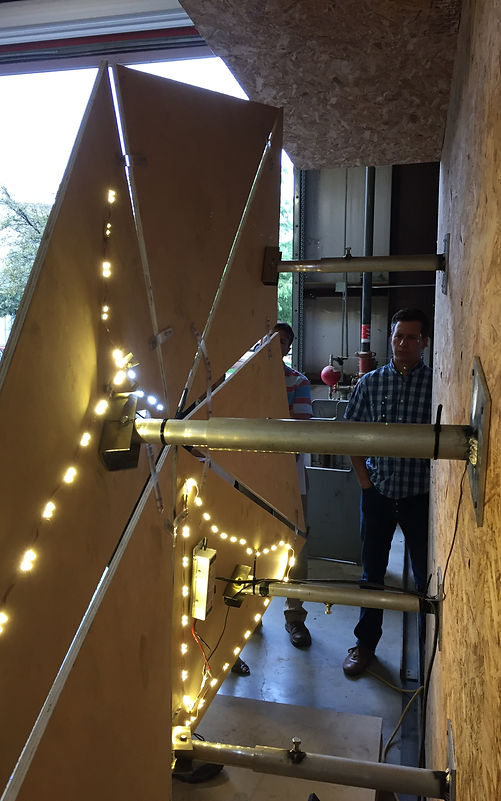

Mock up by Ion Art
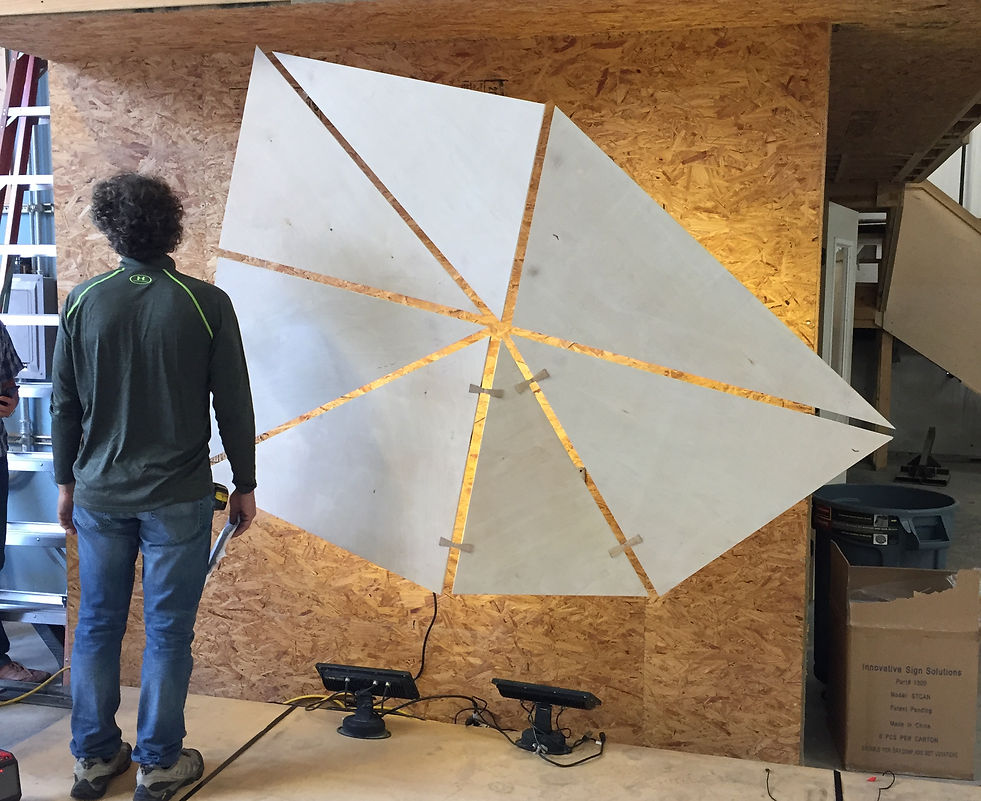



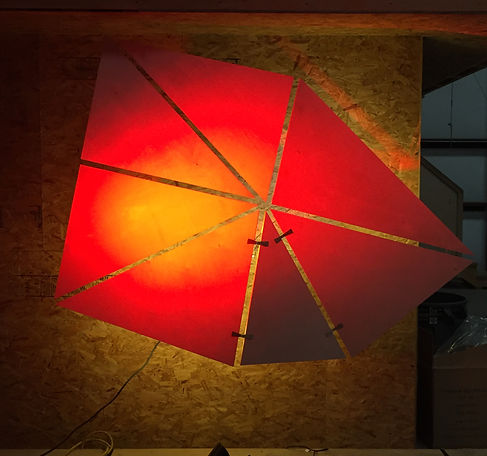
LED light projections
Tree of Life
A grasshopper script was made to take a single curved surface, create a diamond grid panelized surface and offset each panel to create a 1” gap in between each panel. Aluminum telescopic tubes were made by the fabricator, in order to support the panelized surface, either from the existing slab above or from interior steel or concrete columns. The panels were then clipped together by butterfly clips in between the panels to create one rigid singular surface. The intent of offsetting each panel inward to create a gap between the panels is to have LED lights above and below the canopy to change and oscillate through different colors. The plywood panels would act as a backdrop to the LED lights projects on the canopy itself, while also providing light to shine through it.